I took a couple of AN832-4D bulkhead fittings over to my friend Scott's house, where he used his garage full of machine tools to turn them into RV-7 vent exit fittings. Here's an action shot of one of them having a 45-degree cut milled into it, after the threads had already been turned down in one of his three lathes.
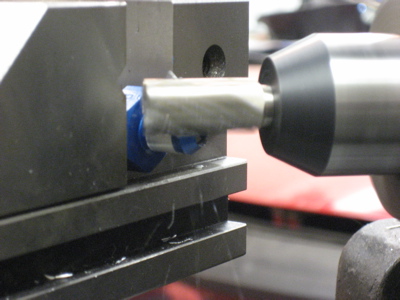
Scott's garage is completely full of huge machine tools and half-assembled motor vehicles. I can only imagine what it will look like in there when he's an old guy and he's had time to really collect stuff.
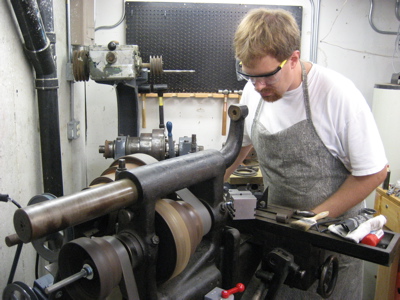
After I got home I polished the ends a bit with the roloc wheel. They came out great. Thanks Scott!
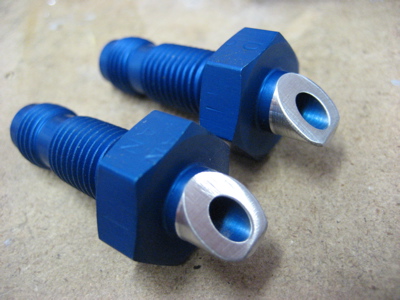
Then I started playing with the plumbing that brings fuel from the tanks to the selector valve. I had already decided to make the run from the valve to the wings in two sections, with a bulkhead union fitting in the middle somewhere. I did something similar on my last RV and it worked out great – it's much easier to bend a perfect fuel line if you can make the two ends independently.
Here's my first idea, which was to put grommets in the inner cover support ribs and locate the unions in the outer ones:
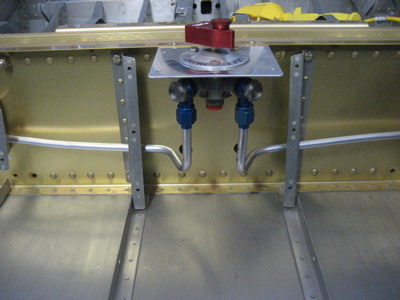
That was relatively easy to make and would have worked well. The problem, though, is that since only the outer cover support ribs are removable (the inner ones are permanently riveted in place) the fuel line would have been held captive once both ends were flared. That would have made maintenance and interior painting a little more troublesome. So, I started playing with the idea of putting the unions in the inner cover support ribs, like so:
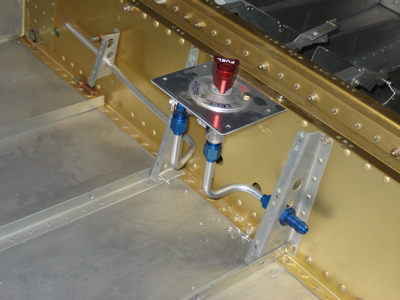
Here's both lines in place. I like this arrangement a lot better.
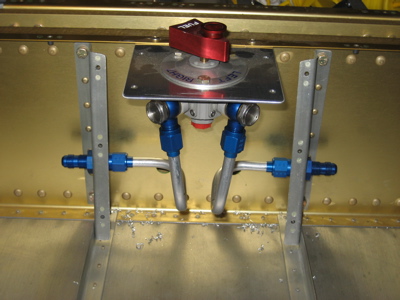
Another shot for posterity. Banjo fittings make life a lot easier.
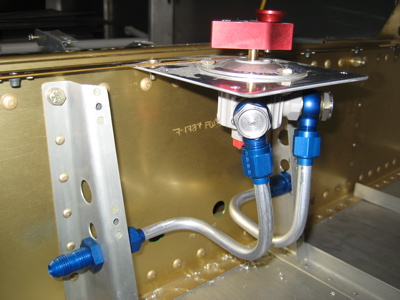
And it all fits within the selector valve cover. Ignore the gap you can see in this photo – this is not an angle from which you'll ever be able to look at the selector valve once the airplane is finished.
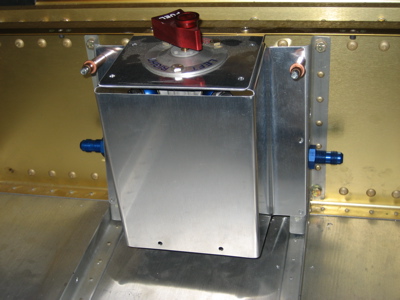
Of course, the photos above make it all seem very easy, but in reality I went through many many iterations before arriving at the final product. Here are some of the previous test pieces that didn't make the cut:
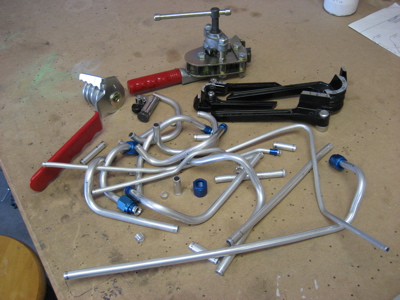
Remember kids, always recycle!
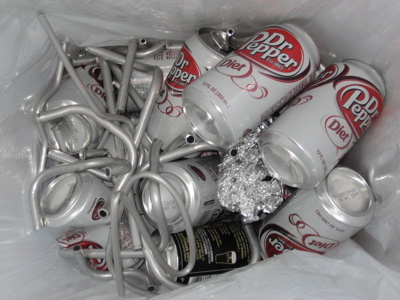
94 degrees inside the shaded garage? No wonder I was feeling parched. Time to knock off for the day and wait for the girl to come home from work.
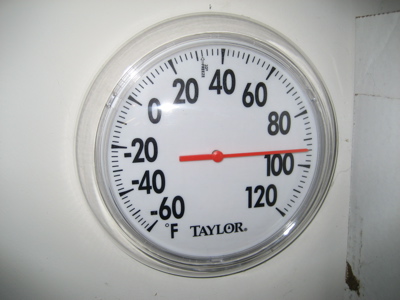