The pitot tube, to be useful, has to be plumbed all the way to the panel… a long journey through a lot of unhelpful structure. I used 1/4" black nylon tubing for pitot pressure and blue for AOA:
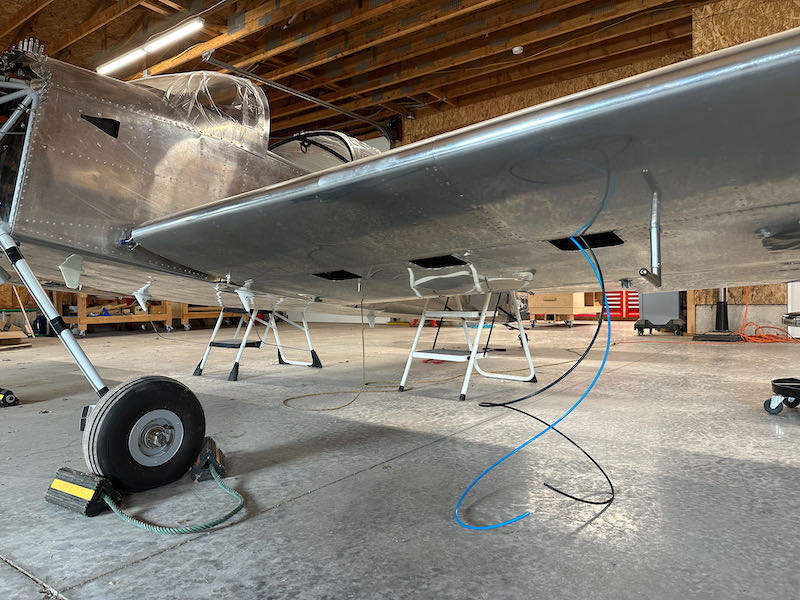
Looking up through the access panel at the plumbing:
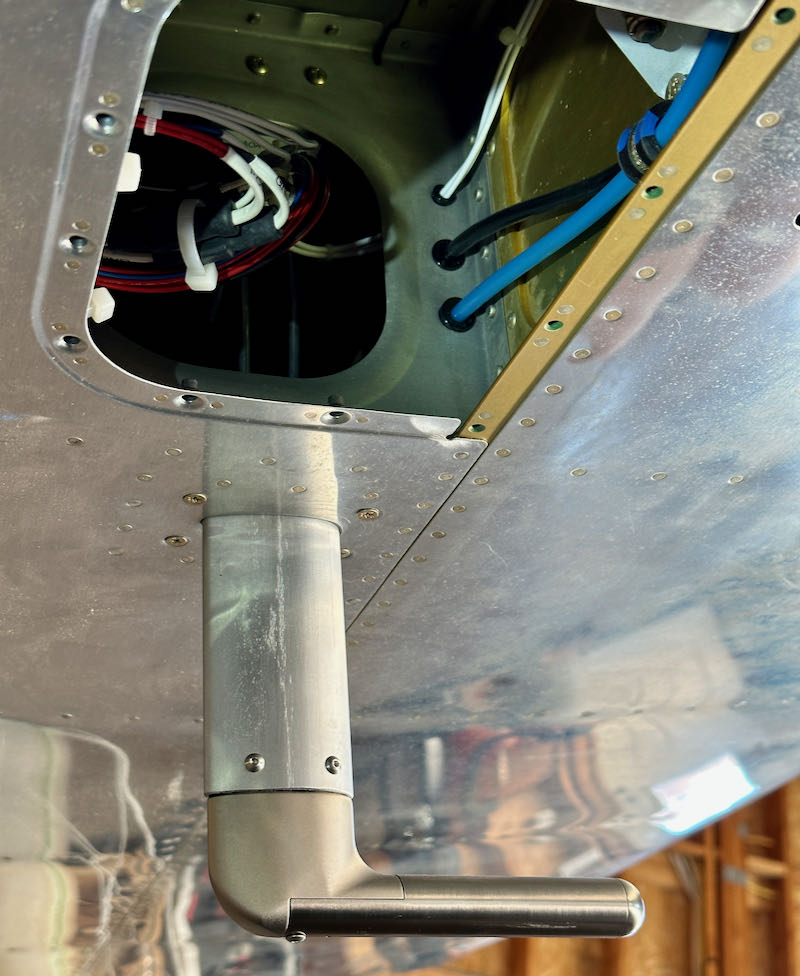
This area is difficult to see or photograph, but the tubes loop around to connect to the previously installed fittings:
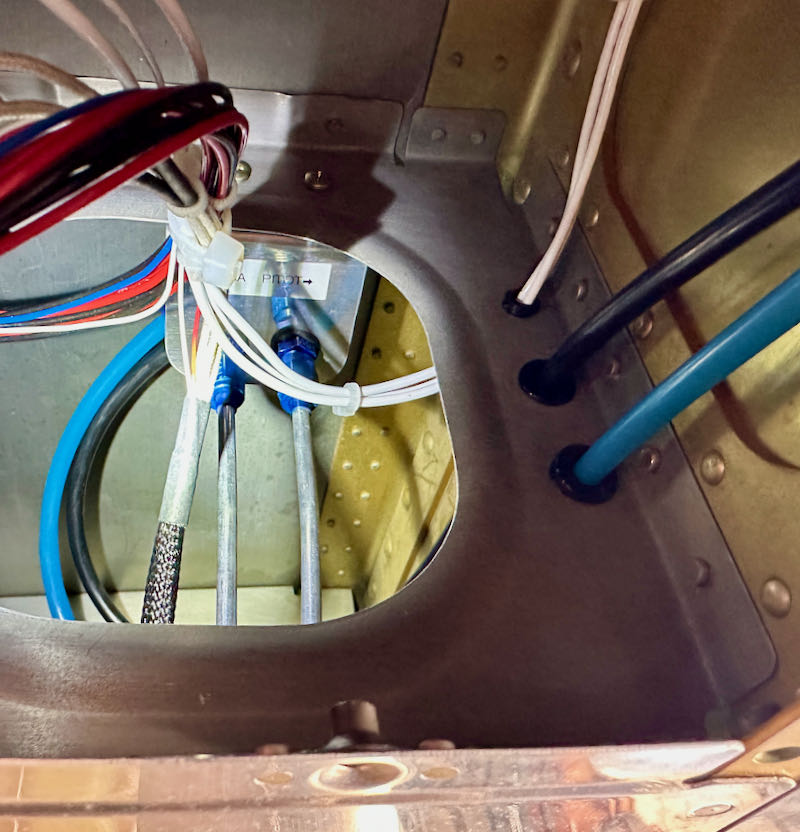
I used a longer bolt and an adel clamp to keep the tubes from fouling the aileron bellcrank:
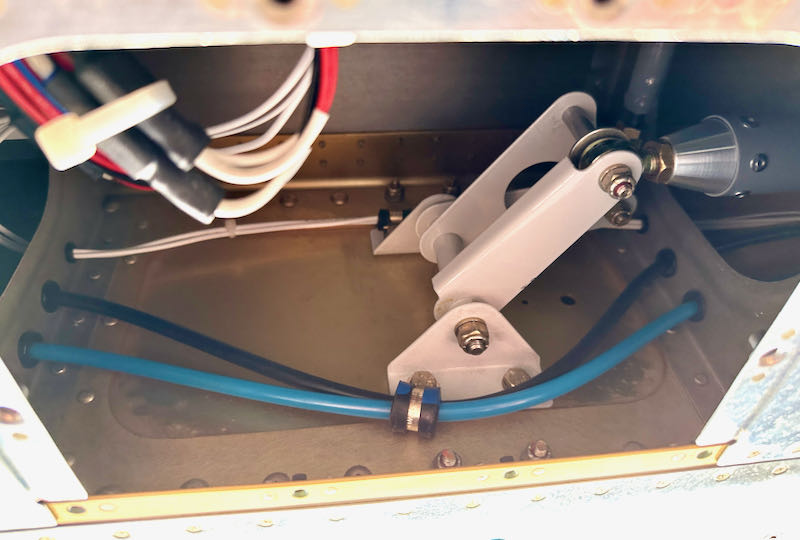
Running the tubing all the way through the wing and into the fuselage was only barely doable! I need a skilled helper with both flexible availability and flexible arms:
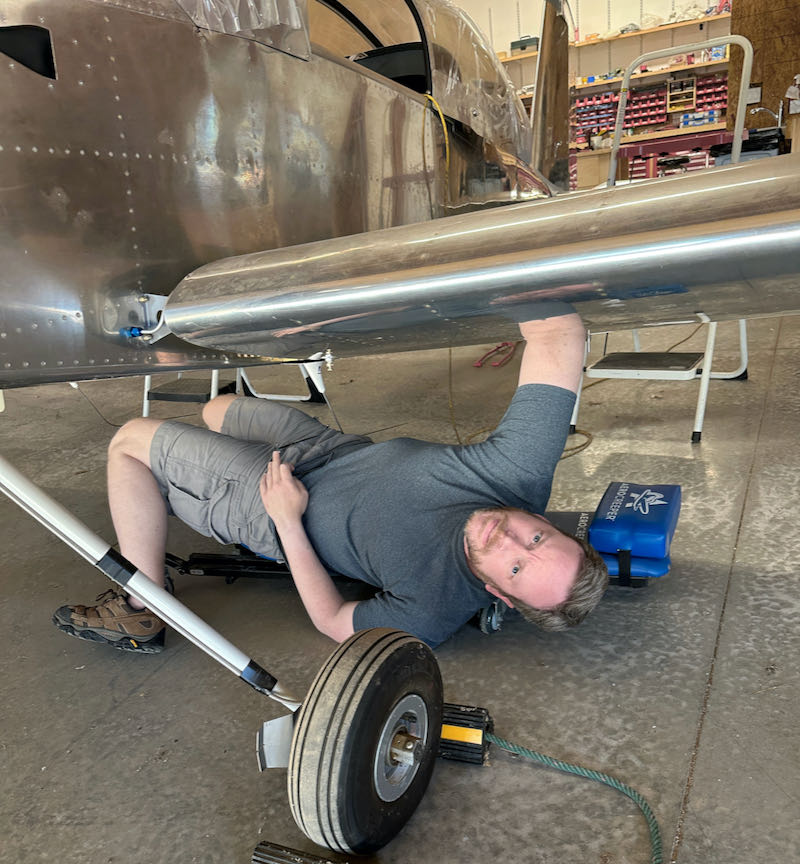
The tubes take an S-turn that's impossible to photograph, then enter the fuselage through the same bushings that allow the wire bundles to pass:
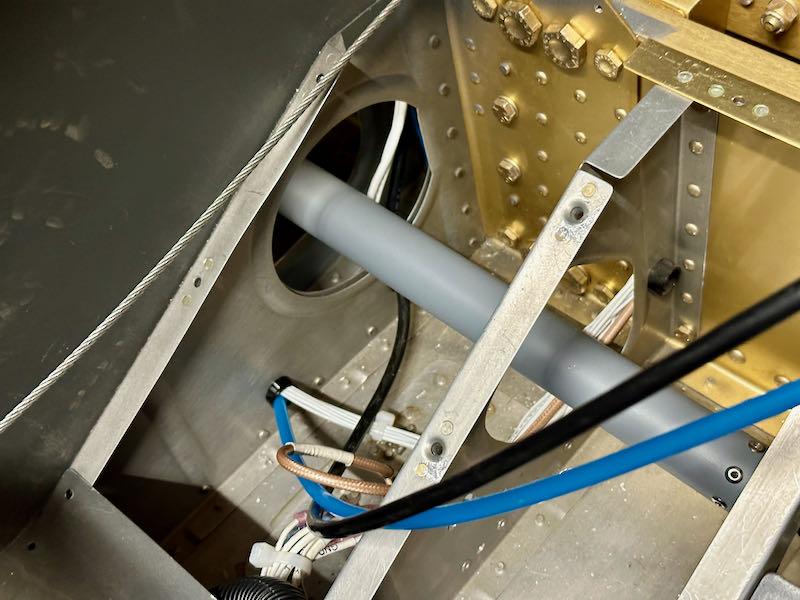
I secured the tubes out of the way of the aileron pushrod, and ran them aft through a protective 3/4" plastic conduit:
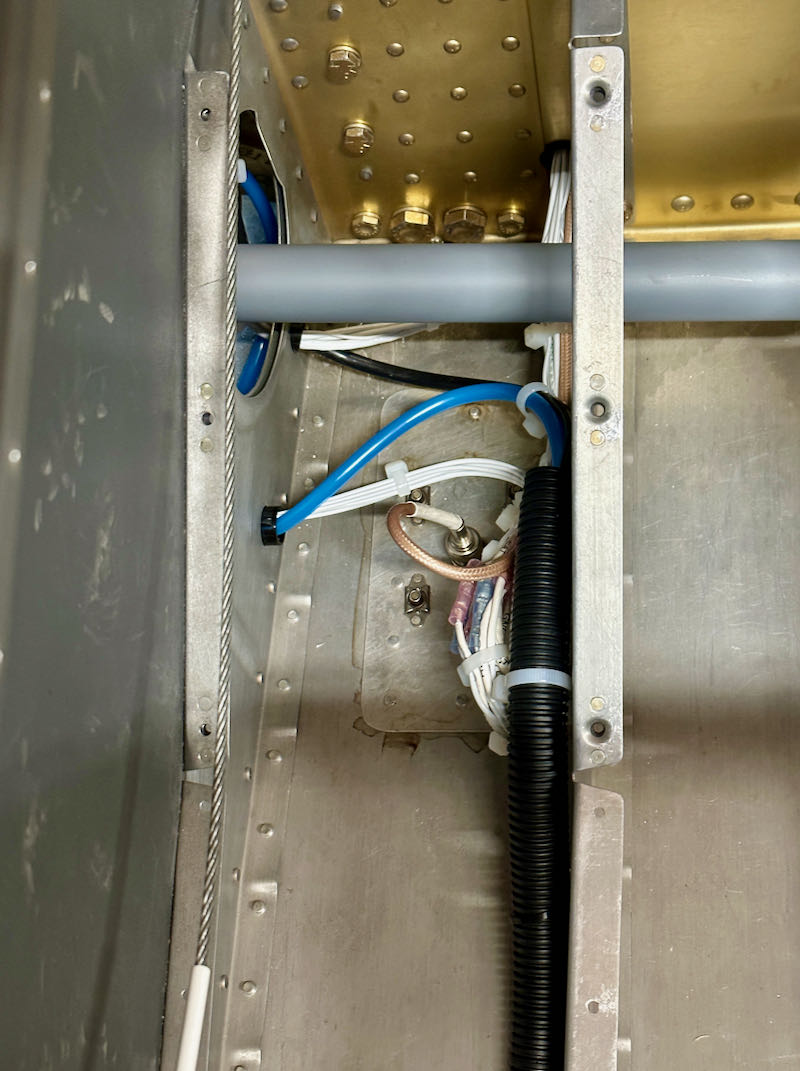
The conduit runs aft under the seat floor, then up the forward face of the F-705 bulkhead:
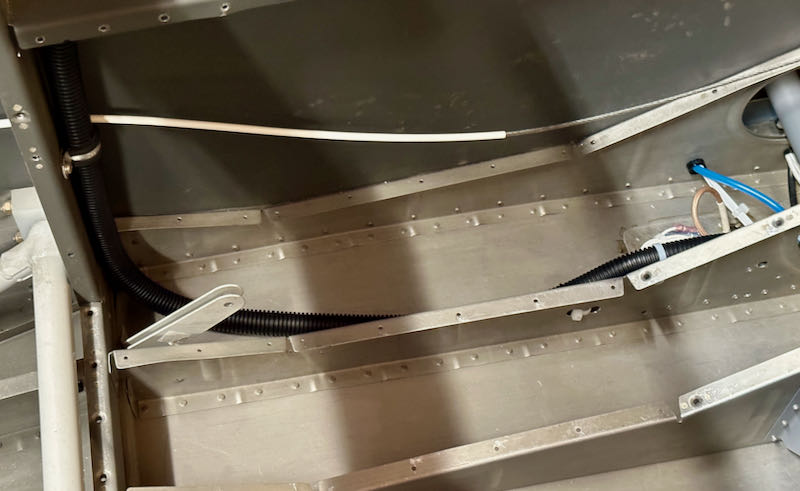
Another adel clamp keeps the conduit out of the way of the rudder cable:
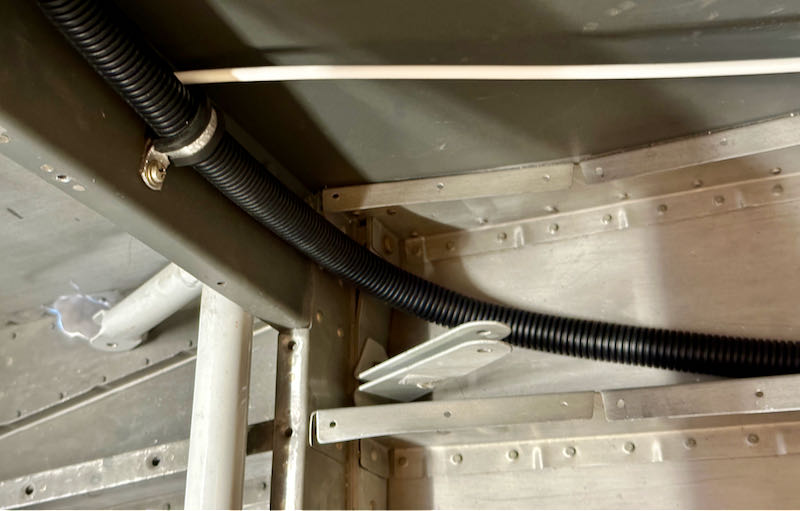
The pitot and AOA tubes, along with the white static tube, pass up through the armrest through a set of plastic bushings. Don't ask me why I chose to use three separate 1/4" bushings here rather than one single larger one. The pitot line (black) goes all the way to the panel, while the static and AOA tubes are cut short here:
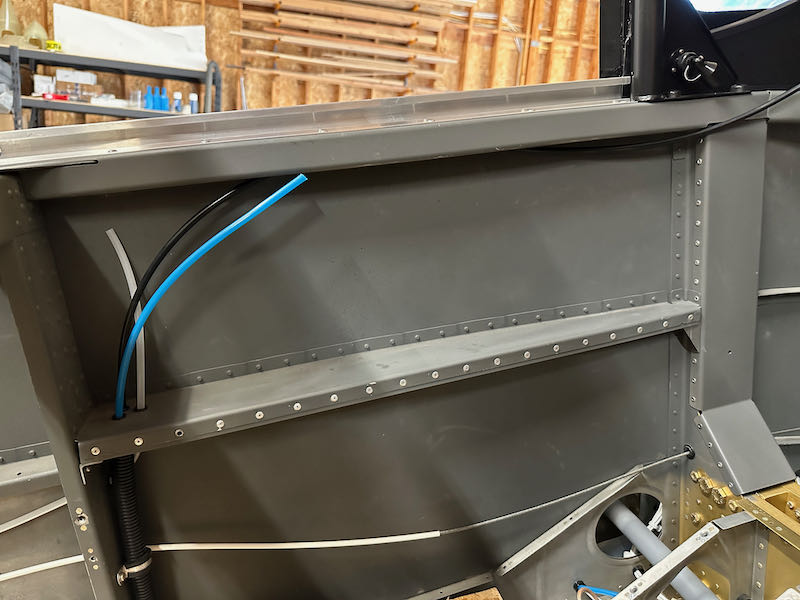
I wrangled the pitot line through a piece of 3/8" conduit, along with two 1/8" tubes for static and AOA. I didn't really want to have to use this tiny tubing size, but due to the space available to run the conduit I had no choice but to use small-diameter plumbing here:
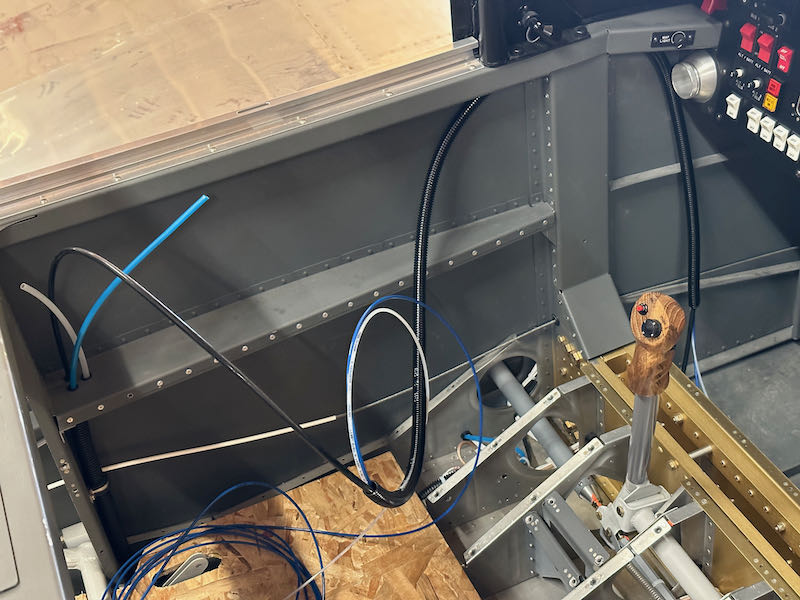
In retrospect I wish I had finished the pneumatic plumbing prior to riveting the center section cap strips. Snaking this conduit over the top of the center section and around the rollbar bolts, without being able to get my fingers on it, was very tough:
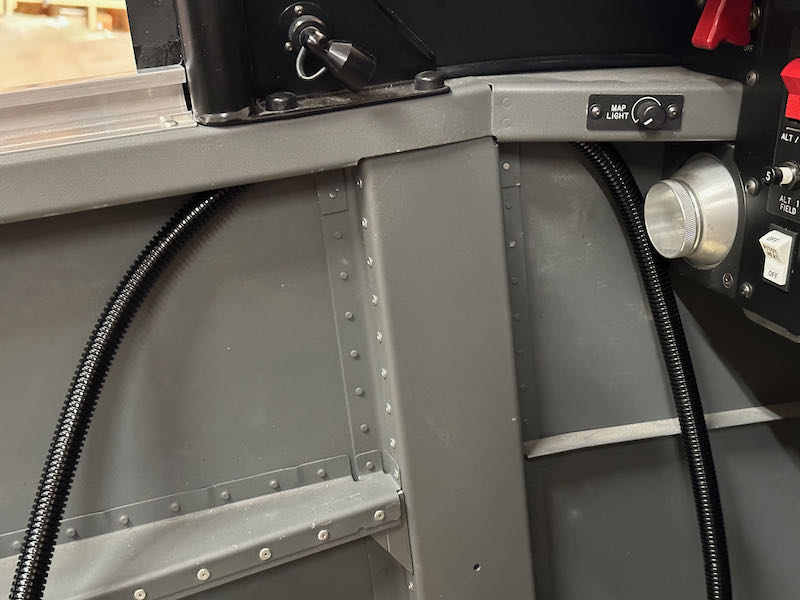
The reducer fittings that convert the static and AOA tubing from 1/4" to 1/8" will be hidden behind the interior panels, aft of the pilot's elbow:
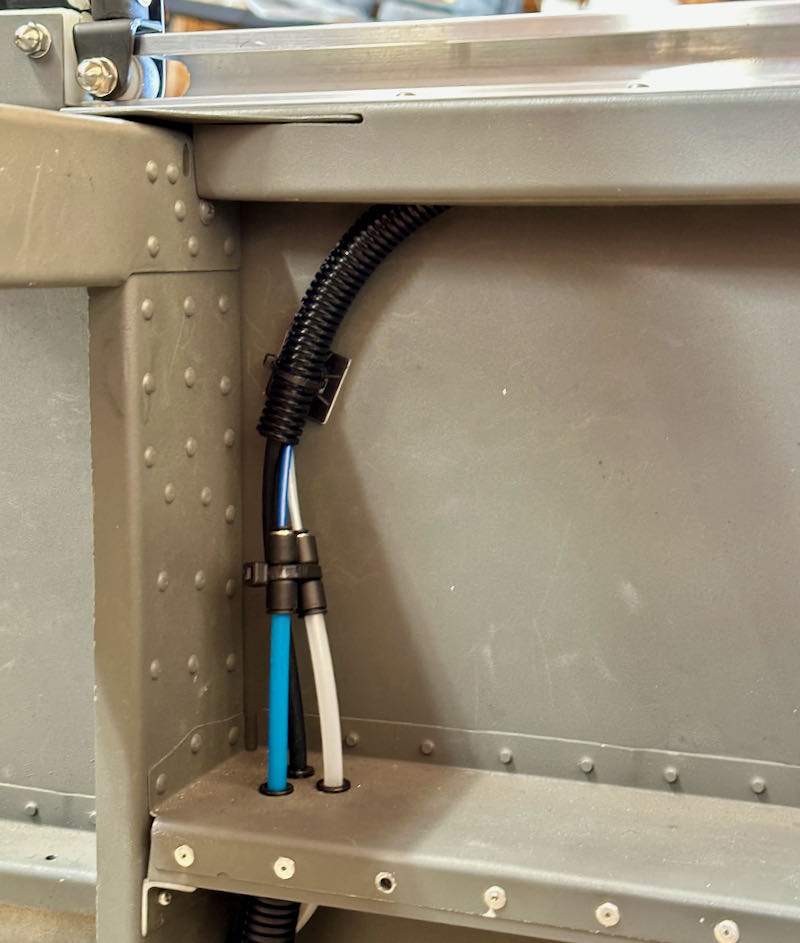
Forward of the panel, the plumbing conduit terminates at an adel clamp screwed to the bottom of the subpanel, and the various tubes branch out from there:
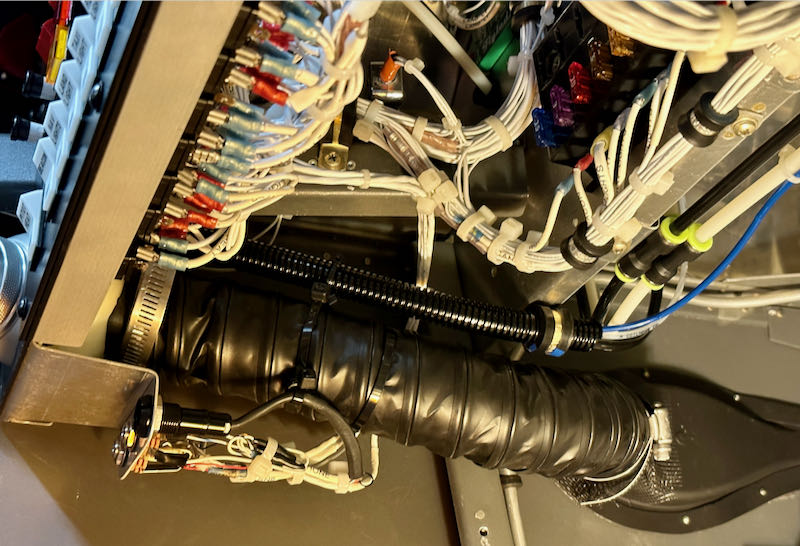
This photo is looking up at the bottom of the subpanel, with the nose of the airplane towards the bottom of the picture. I had previously done most of the under-panel plumbing prior to riveting on the forward top skin, but in my haste neglected to document it. Tee fittings are screwed to the subpanel flange with little brackets I made from scrap, and an adel clamp or two keeps everything constrained. To this I zip-tied the AOA tube, adapter-ed back up to 1/4" interface with the #2 ADAHRS:
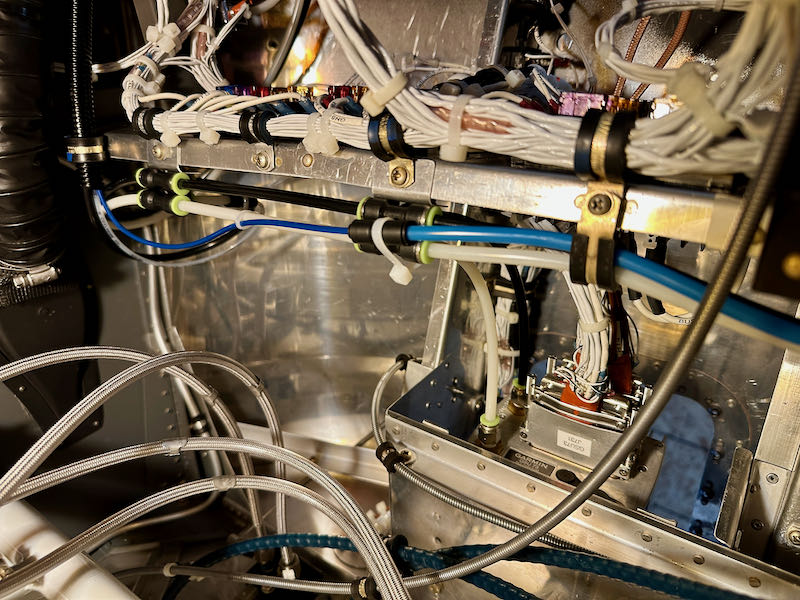
One branch of the plumbing brings pitot and static to the G5 backup instrument, as well as connecting to the alternate static port:
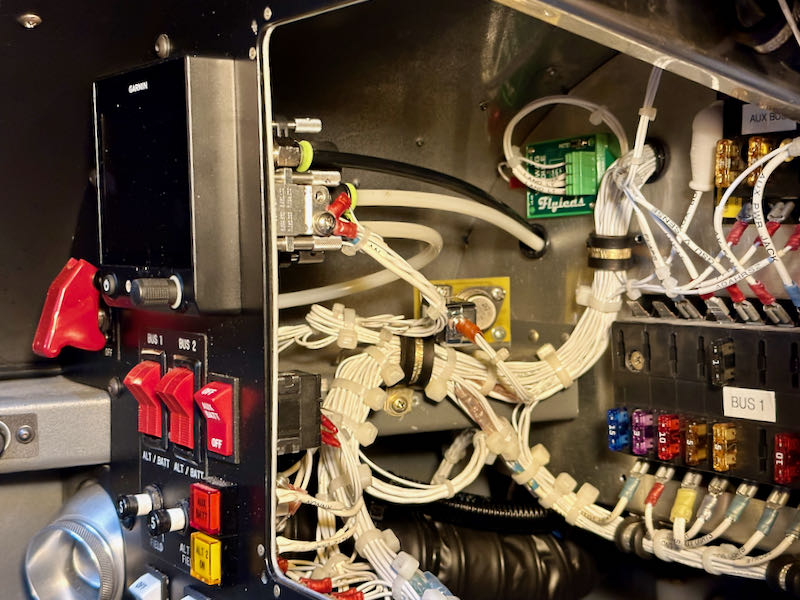
The #2 ADAHRS lives underneath the radio stack, and is difficult to photograph, but it now has all three of its pneumatic ports plumbed:
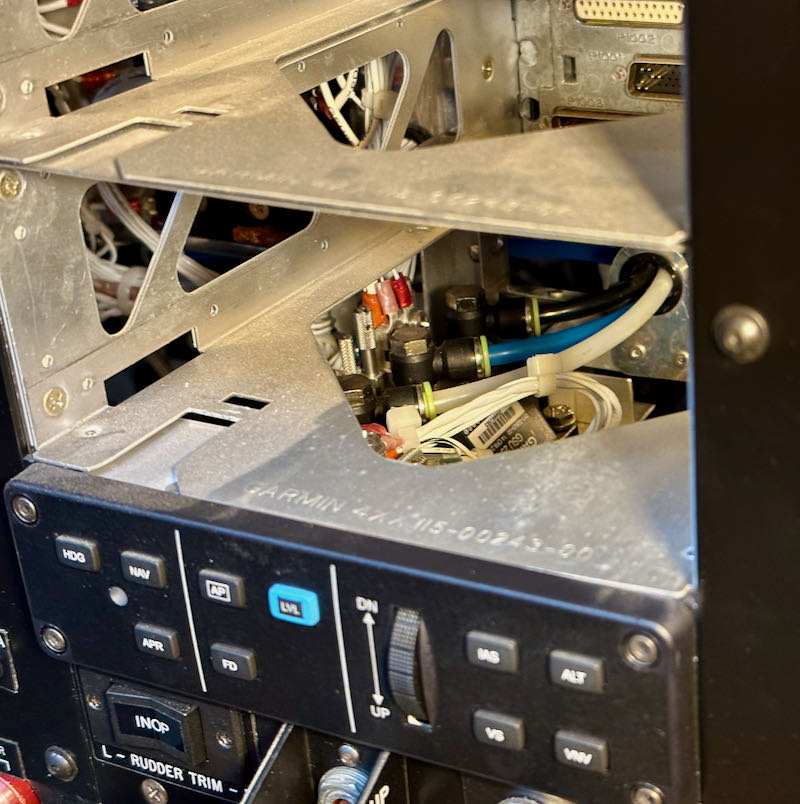
I have no good way to leak-check any of this plumbing, but I did apply lung pressure to the pitot tube and suction to the static ports, and confirmed the expected results on the cockpit displays. So that's good enough for me to call the instrumentation air plumbing complete.